AI Art Meets Real-Life Construction
- Youtube Views 5,679 VIDEO VIEWS
This article contains paid promotion for Sandvik.
THIS real-life statue was made with artificial intelligence.
Dubbed the “Impossible Statue”, this project was made by combining the works of five different historical artists using AI. At 150cm tall, weighing 500 kg carved from stainless steel, the sculpture showcases just how far technology has come and its ability to transform the future of how we build our world.
The ultimate test of engineering precision
Sandvik is a global company that is a world-leader within component manufacturing due to its unique position with leading offerings of cutting tools and software solutions. They wanted to challenge some of their best engineers to create the ultimate pressure test of precision, skill, and advanced engineering – and so the Impossible Statue was born.
Now this isn’t just an art project. The way this sculpture was designed and built demonstrates how digital solutions, digital twins and state-of-the-art tools could have huge impacts on manufacturing of the future – improving efficiency and reducing waste by connecting all steps in the manufacturing process.
In the field of manufacturing, verification is a key factor in order to ensure all parts fit together during final assembly. Think about the precise dimensions of a car door necessary to close properly, the measurements of a knee implant required to comfortably place in a patient’s leg or the installation of doors and windows in a building.
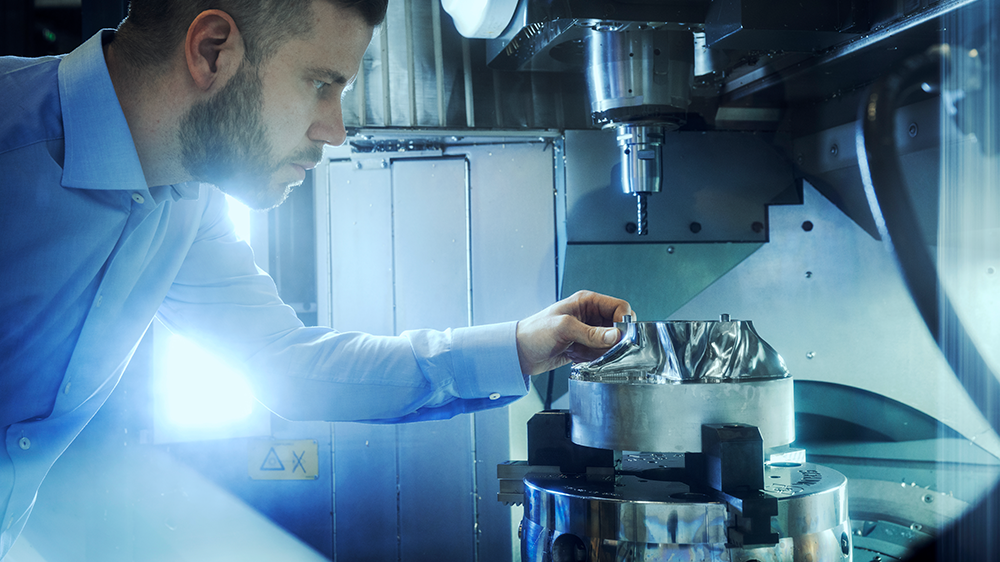
Above: An engineer in the beginning stages of creating the statue. Image courtesy of Sandvik.
Conventional verification - which is essentially manually measuring each individual component of a product - in some projects can take up to 30 minutes. It’s a make or break part of the design process. If one part doesn’t fit precisely in the assembly, the whole product might not work. But with Sandvik’s technology, this process can be done in just 30 seconds.
When it comes to manufacturing, a standard computer algorithm follows a specific set of step-by-step programming instructions. Once the task is completed, it stops functioning. But an AI algorithm doesn’t follow inputted instructions. Instead, it focuses on ‘machine learning’ by learning the most optimised way to perform a task using input data and feedback acquired through millions of rounds of repetition.
Today, AI is mostly applied for quality control and predictive maintenance for manufacturing.
Building the Impossible Statue
AI tools Dall-E, Stable Diffusion and Midjourney were used to study the works of Michelangelo, Rodin, Augusta Savage, Kathe Kollowitz and Kotaro Takamura. Each of these recognizable sculptors incorporated distinct genres of art from around the world during different eras of time.
A few weeks later, an image was created which appeared as a rough sketch of a 2D silhouette of a man holding out his hand. Then came the challenge of turning that initial sketch into a 3D model. The image was updated to become more detailed with parts clearly inspired by the various inputted artists.
The most difficult part was figuring out what the back side of the statue should look like. Engineers at Sandvik did this by using human pose-estimators to add to its initial point clouds, creating what was a complete and symmetric body shape. They used video-game algorithms and AI models to re-create invisible fabric and final details on the project.
Vericut®, which is Sandvik machining simulation software, was used to run virtual tests on a digital twin before anything was physically built, ensuring the actual machining process could be carried out flawlessly.
Digital twins are already used all across the construction industry to create replicas of real-world spaces during the initial planning stages with similar cost and time saving goals.
Once the 3D model was complete, the team programmed around 40 million lines of G-code, which is the operational language that tells machines what to do. This code was inputted into a computerised manufacturing machine using MasterCam® software.
Above: Engineers programmed around 40 million lines of G-code during the production process. Image courtesy of Sandvik.
On the Impossible Statue, this digital modelling led to no components being scrapped due to error, because they had all been digitally perfected before the start of machining.
And the precision between the statue and 3D model is less than 0.03mm in deviation. That’s a level of precision demanded in, for example, manufacturing of Swiss watches.
Is this the future of construction?
The Impossible Statue exemplifies how AI has the potential to transform the manufacturing industry.
AI can enable engineers to create a more sufficient and sustainable method of production by improving decision making, extending equipment life, and cutting down costly downtime. By studying components ahead of time, it can significantly decrease all possible errors that could make for expensive fixes.
The tools available now are really only scratching the surface of the possibilities – from 3D models to helping prevent project overruns and even mitigating safety risks on site. And as AI advances, it is bound to become even more of an integral part in manufacturing projects.
To learn more about Sandvik's investment in AI manufacturing, click here.
Additional footage and images courtesy of Sandvik.
We welcome you sharing our content to inspire others, but please be nice and play by our rules.