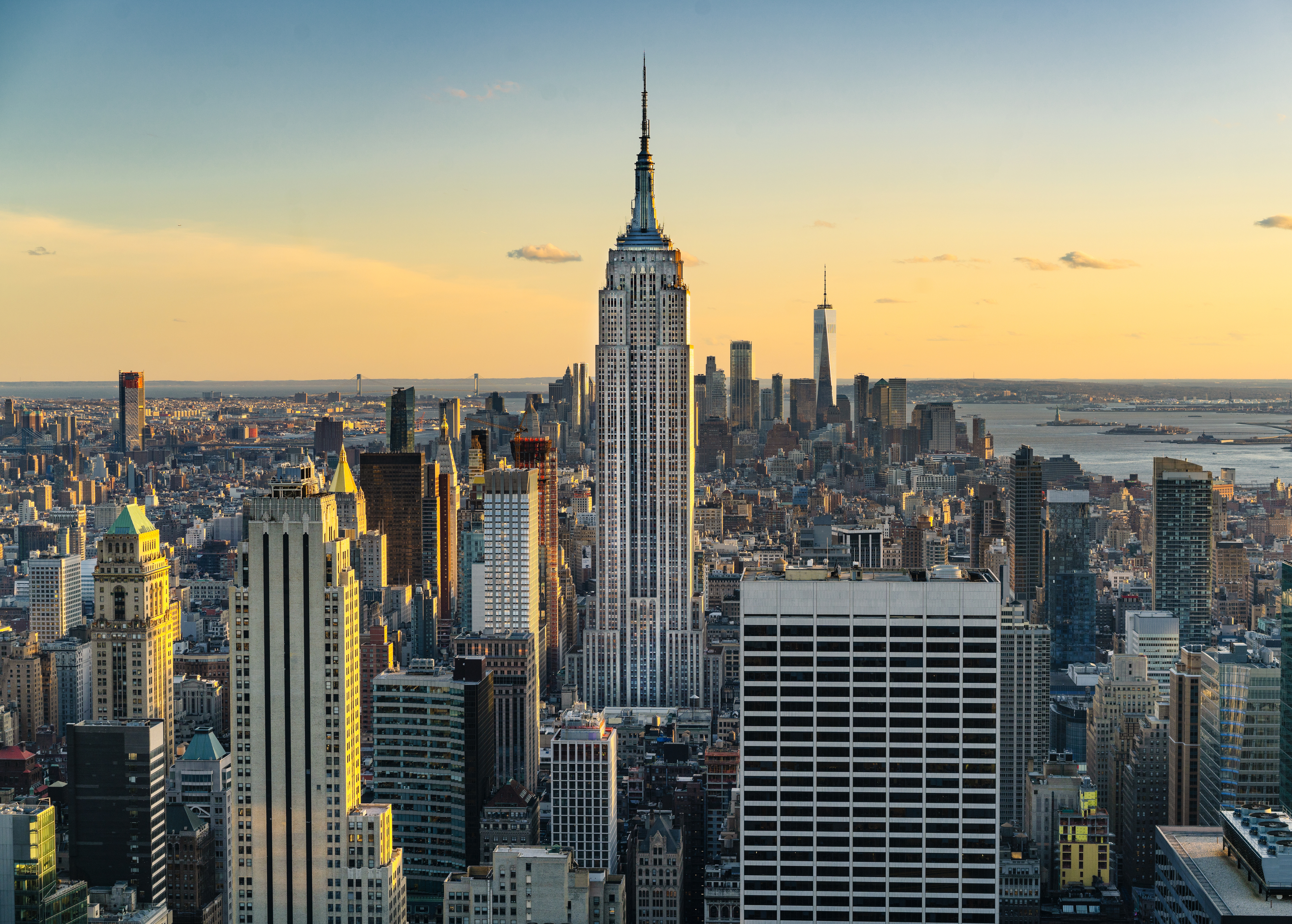
Why Can’t We Build as Fast as the Empire State Building?
This article contains paid promotion for Buildots.
TO THIS DAY it remains an astonishing feat of engineering.
New York’s Empire State Building was constructed in just one year and 45 days, dramatically rising 102-storeys above Manhattan to quickly claim the title of world’s tallest building – a record it would go on to hold for nearly 40 years.
Though it eventually lost its title to the original World Trade Center towers in the early 1970s, the Empire State Building’s cultural significance has endured far longer. It’s a New York icon that’s appeared relentlessly throughout pop culture.
It’s something of a landmark for the construction sector too.
Tales of the building’s record-breaking construction schedule go hand-in-hand with most descriptions of it and seemingly haunt the industry. I have lost count of the number of times I have seen people point to it in speeches or conversations and ask “why can’t we build that fast today?”
Above: New York’s Empire State building under construction in 1930.
To properly answer that you need to look at two things: firstly, what the team behind the Empire State Building did to deliver it so quickly, and second what we’re doing in today’s construction sector that’s different.
So let’s wind it back to 1930s New York.
This was a unique place – one grappling with the onset of the Great Depression amidst a changing skyline that had become a key battleground in the so-called “Race for the Skies”.
US businessman John Jakob Raskob found himself committed to that race but in a rapidly changing economic landscape. He was determined to build the Empire State taller than 40 Wall Street (283-metres) and the recently-completed Chrysler Building (319-metres), but he needed to move quickly. With the markets in free fall, Raskob needed his skyscraper finished and bringing in money as quickly as possible.
Racing for the Skies
Speed was the name of the game from day one. Raskob appointed Shreve, Lamb and Harmon as architects with Starrett Bros and Eken as lead contractor, who in turn coordinated with over 60 sub-contractors.
Above: A steel worker building the Empire State, high above the streets of New York.
Construction works began before the design was completed. Foundations were excavated while demolition of the existing building was still going on. The steel frame was erected in a highly-choreographed work sequence that minimised even a moments' downtime, and railway tracks were used to move materials. Storage was optimised. Deliveries were made just in time. At one point contractors added 14-storeys to the superstructure in just 10 days.
The client had one goal and the project team understood it, clear as day.
Building in 2023
The contrast with today couldn’t be more stark – or frustrating. We know more about these processes and ways of working now than we’ve ever done yet the prize of unlocking new levels of productivity in construction remains elusive. The Empire State’s 90-year-old benchmark still thrust at us with nauseating regularity.
Of course much has actually improved since the 1930s. Some 14 people lost their lives during construction of the Empire State (though unofficial numbers are thought to be much higher). Safety today has been transformed. We now build more sustainably. Our labour practices are better.
But while many schemes are successful, it’s common for the world’s biggest and most-newsworthy construction projects to find themselves late and over-budget. London’s Elizabeth Line, Berlin’s Brandenburg Airport, New York’s East Side Access Project – the list isn’t a short one.
Above: London’s Elizabeth Line, then under construction by Crossrail. Image courtesy of Crossrail.
And for all those that make the news – or get immortalised in a video on The B1M – there are hundreds more that we don’t hear about. Hundreds of companies are losing money, missing their margins and feeling the pressure. Hundreds of clients are being left disappointed.
So what’s the issue?
Well, it goes much deeper than merely the “increased complexity” of projects. Yes, our schemes are more complicated and more technologically advanced today than ever. They’re supported by international supply chains and are often at the mercy of a deeply interconnected, globalised economy.
But talk to experts or examine the research papers and the problems all seem to stem from a lack of detailed visibility on our projects.
There are lots of data points yet we only principally seem to measure programme, budget and safety. Those areas are of course critically important, but they don’t tell us the full picture of what’s really happening at the more granular level.
Frankly most projects don’t go to the same degree of detailed analysis or planning that we saw on the Empire State. But we now have a new tool at our disposal: technology.
You Can’t Improve What You Can’t Measure
New innovations are enabling us to monitor projects in real time, gathering powerful datasets that show where inefficiencies are happening. As the saying goes: you can’t improve what you can’t measure – but now we can measure. We can see issues that we haven’t been able to really see for decades.
Construction-tech firm Buildots has been helping construction companies to completely automate progress tracking by using wearable 360-degree cameras and an AI model to capture project data and compare it to the original design and schedule. Their solution provides companies with an objective dataset that shows what’s really happening on their sites, which enables teams to make fact-based decisions and enhance progress control.
The firm’s recent research looked at 64 different types of projects across the US, UK, Canada, EU, Japan, and Israel, identifying inefficiencies in four key areas that are often overlooked.
Above: Buildots’ research initially found inefficiencies in four areas. Image courtesy of Buildots.
The study found that roughly 10% of activities started on-site are not completed during the first visit. That means trades regularly need to return to the site to finish their tasks, creating delays.
There’s also a shocking inconsistency in trade output week-to-week. Of course, weekly output can be affected by anything from the weather to design changes or incomplete work from previous trades. But the output of each trade fluctuates by 56% week-to-week on average. One week a trade could complete 10,000 square feet, and just 4,400 square feet the next.
Another major factor causing project delays is when activities are started out of order. There’s always going to be some degree of this thanks to the construction industry’s dynamic nature. But, as the study is showing, too many sequence deviations can cause a domino effect on the rest of the project. The study found that nearly 10% of activities are performed out of sequence.
The next Empire State Building is unlikely to emerge from an industry like this, but now we can see why that is and begin to improve.
It’s technology that’s enabled us to find these issues and technology that can help give us the edge in finally improving our productivity.
Above: Research by Buildots found a correlation between the number of return visits made to a work area and overall project delay. Image courtesy of Buildots.
Of course, anyone in construction will tell you that many factors contribute to making a project successful. Effective teams, strong client direction, clear shared-objectives, communication, planning and a solid supply chain are just as instrumental to project success today as they were in 1930s New York. Emerging technologies must support and enhance our work in those areas.
But in such a tough market and with such tight margins, tech could be what makes the difference.
Above: The Empire State Building’s construction schedule remains legendary.
It could also help firms become more resilient to the events that batter them. Construction is notoriously volatile. Throw in a pandemic, global supply chain crisis and economic downturn and you’re approaching something close to hell.
An enhanced, more granular approach to data can help underpin an organisation’s VUCA strategy – its ability to handle volatility, uncertainty, complexity and ambiguity – something that’s essential for construction businesses, especially in 2023.
It’s a year in which we now have the tools and ability to see issues that we couldn’t really see before. Buildots’ report serves as a crucial benchmark for firms all over the world to assess their project performance and identify opportunities for improvement. Almost a century on from its construction success, the Empire State could finally be eclipsed by what we build next.
Learn more about construction’s hidden inefficiencies and how to find and measure them in this free whitepaper by Buildots.
There's also the chance to dive deeper in our free live event [watch below].